Die Sonplas GmbH, etablierter Anbieter hochwertiger Montage- und Prüftechnik für die Automobilindustrie, leistet mit einem neu entwickelten Verfahren zur Bearbeitung von Elektroden einen Beitrag zu einer effizienteren und nachhaltigeren Produktion von Batteriezellen für die boomende Elektromobilität.
Als langjähriger Partner der Automobilindustrie ist die Sonplas GmbH aus Straubing bestens mit den hohen Qualitätsansprüchen dieser Branche vertraut. Seit mehr als 10 Jahren setzen die Ingenieure von Sonplas mit ihren innovativen Ideen nun auch Impulse in Sachen Qualität im Bereich der Elektromobilität.
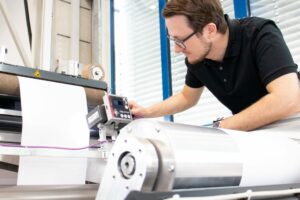
Rolle-zu-Rolle-Demonstrator zum Schneiden von Elektrodenblättern. Dabei werden die Elektroden-Folien abgewickelt, mit dem Laser zugeschnitten und wieder aufgewickelt oder vereinzelt gestapelt.
Das niederbayerische Unternehmen mit mehr als 300 Mitarbeitern entwickelt, baut und liefert seit fast drei Jahrzehnten maßgeschneiderte, innovative Prüf- und Montageanlagen für die Automobil-, Automobilzuliefer-, Elektronik- und Luftfahrtindustrie.
Neben der Montage von Rotoren, Invertern und anderen Komponenten für elektrisch angetriebene Autos und Nutzfahrzeuge, beschäftigt sich Sonplas mit der Herstellung von Batteriezellen für sowohl automotive als auch non-automotive Anwendungen. Ein wichtiger Aspekt dabei ist, optimierte Schnittkanten bei der Elektrodenerstellung für Batteriezellen zu erreichen, um mit einem neuen Qualitätsniveau „Made in Germany“ der internationalen Konkurrenz, allen voran den etablierten Marktbegleitern aus Asien etwas entgegenzusetzen.
Derzeit entsprechen die in den Zellfabriken angewendeten Fertigungsmethoden und Standards zur Bearbeitung von Lithium-Ionen-Batteriefolien oft noch nicht dem für die Automobilindustrie notwendigen Qualitätsniveau. Von der Steigerung der Qualität, vor allem der Schnittkante und der Vermeidung von Partikeln hängen unmittelbar die angestrebte Ausschussquote bei der Herstellung, verbesserte Güte und eine verlängerte Lebensdauer der Zellen ab. Sonplas hat hierzu einen neuen Ansatz beim Laserschneiden und eine darauf abgestimmte Absaugung entwickelt.
Optimaler Laserschnitt an Elektrodenfolien
Derzeit kommen bei der Herstellung der Lithium-Ionen-Batterien in der Elektromobilität drei Zellformate zum Einsatz: Die Pouch-, die zylindrische sowie die prismatische Zelle. Unabhängig vom Zelltyp besteht die kleinste Einheit jeder Lithium-Ionen-Zelle aus zwei beschichteten Folien, den Elektroden. Zum einen eine beschichtete Kupferfolie für die Anode und zum anderen eine beschichtete Aluminiumfolie für die Kathode. Bei der Elektrodenfertigung werden diese Trägerfolien auf großen, sogenannten Mutterrollen mit Elektrodenmaterial beschichtet. Und anschließend auf Tochterrollen separiert, um die gewünschten Formate der Zellen zu bekommen. Im nächsten Schritt werden die Tochterrollen am Rand beschnitten (Notching) bzw. die einzelnen Elektrodenblätter ausgeschnitten (Separation). Im Vergleich zu den vielfach noch verwendeten mechanischen Stanzverfahren bringen moderne Laser-Systeme deutliche Vorteile im Hinblick auf Qualität, Flexibilität und Betriebskosten.
Auf Schnelligkeit, Sauberkeit und Flexibilität kommt es an
Demonstrationsanlage am Hauptsitz der Sonplas GmbH in Straubing. Hier haben Kunden die Möglichkeit, Versuche mit Kundenmaterial durchzuführen.
Um die Produktivität zu erhöhen, wird üblicherweise das Schneiden (Notching) der Batteriefolien im Rolle-zu-Rolle-Verfahren durchgeführt. Dabei gibt es anspruchsvolle technische Probleme zu lösen. Florian Thalhofer, Entwicklungsingenieur bei Sonplas, beschäftigt sich mit diesem Prozess bereits seit mehreren Jahren: „Die eigentliche Problematik liegt in der Kombination, der verschiedenen Herausforderungen. Wir haben eine sehr hohe Schnittgeschwindigkeit bis deutlich über 1 Meter pro Sekunde. Es darf zu keiner Verschmutzung der Elektroden kommen. Vor allem nicht mit Partikeln, die größer als 10 µm sind, da sonst die Separator-Folie leicht durchstoßen werden kann. Zudem braucht es ein System, mit dem wir unterschiedliche Geometrien ohne Anlagenumbau bearbeiten können, wie z. B. die größten marktüblichen Elektroden im Bearbeitungsbereich von 700 x 700 mm und darüber hinaus.“ Ein hochkomplexer Vorgang, der höchste Präzision bei hohen Geschwindigkeiten erfordert und gleichzeitig flexibel und anpassbar sein muss.
In einem umfangreichen Innovationsprojekt, das zusammen mit wissenschaftlichen Instituten und Partnern aus der Industrie durchgeführt wurde, konnte ein innovativer Laserprozess mit einem neuartigen Ansatz bei der Absaugung entwickelt werden.
Florian Thalhofer: „Uns war es unter anderem wichtig, die sogenannte HAZ (Heat affected zone), sprich die Wärme-einflusszone, auf das Material zu verringern. Beim Schneiden sollte es zudem weder zu einem sogenannten Burnback, einem Abbrand der Beschichtung, oder einer Gratbildung kommen. Und auch die Partikelgröße und Partikelanzahl wollten wir verringern.“ Wie die Ergebnisse zeigen, konnte diese Zielsetzung erreicht werden. Dabei steht der neuartige Prozess für Kunden für Evaluierungen oder Musterprodukten nicht etwa nur unter Laborbedingungen zur Verfügung, sondern auch in einer produktionsnahen Proof-of-Concept-Anlage. „Durch den besseren Schnitt bei den Elektrodenfolien machen wir die Produktion nachhaltiger und erhöhen die Lebensdauer der Batteriezellen,“ freut sich Paul Birkeneder, bei Sonplas im Vertrieb. Außerdem hat das Unternehmen ein Verfahren zur allgemeinen Beurteilung der Güte von Elektrodenschnitten anhand von messbaren Qualitätskriterien entwickelt. Eine entsprechende automatische Inspektions-Station steht auch für Evaluierungen mit Kunden zur Verfügung.
Der Straubinger Sondermaschinenbauer Sonplas GmbH arbeitet bei der Entwicklung des Laserprozesses mit der RAYLASE GmbH zusammen.
Durch die Kombination des Know-hows der Niederbayern im Sondermaschinenbau mit den innovativen Laserablenkeinheiten der Oberbayern ist es den zwei forschenden Unternehmen gelungen, einen qualitativ hochwertigen Laserschnitt an den zu separierenden Elektrodenfolien zu erreichen. Das stützt nicht nur das derzeit hochdynamische Wachstum der Batterieproduktion in Europa und vor allem in Deutschland, sondern verbessert auch die ökologische und ökonomische Bilanz der Herstellung. Denn die bessere Qualität hilft, die derzeit großen Ausschussraten bei der Zellproduktion zu reduzieren.
- Beidseitig beschichtete Graphit-Anode von 260 µm Dicke vorher
- Nachher: Das Ergebnis von Sonplas – eine klare Kante ohne Abbrand.
- Nachher mit Sonplas: keine Schmelzperlen und geringere Wärmeeinflusszone.